1. Aluminum alloy
Aluminum alloy has excellent strength-to-weight ratio, high thermal and electrical conductivity, and natural corrosion protection. They are easy to process and have low batch costs, so they are usually the most economical choice for manufacturing custom metal parts and prototypes. Aluminum alloys are generally lower in strength and hardness than steel, but they can be anodized to form a hard protective layer on their surface.
Aluminum 606 is the most common and universal aluminum alloy with good strength-to-weight ratio and excellent machining performance.
Aluminum 608 has similar composition and material properties as 6061. It is more commonly used in Europe because it complies with British standards.
Aluminum 7075 is the most commonly used alloy in aerospace applications. In aerospace applications, weight reduction is essential because it has excellent fatigue properties and can be heat treated to the same high strength and hardness as steel.
Aluminum 5083 has higher strength and excellent seawater resistance than most other aluminum alloys, so it is commonly used in construction and marine applications. It is also the best choice for welding.
2. Stainless steel
Stainless steel alloys have high strength, high ductility, excellent wear resistance and corrosion resistance, and are easy to weld, process and polish. According to them, they can be (essentially) non-magnetic or magnetic.
Stainless steel 304 is the most common stainless steel alloy with excellent mechanical properties and good machinability. It can resist most environmental conditions and corrosive media.
Stainless steel 316 is another common
stainless steel turned parts with mechanical properties similar to 304. Although it has higher corrosion resistance and chemical resistance, especially for salt solutions (such as sea water), it is usually the first choice for applications in harsh environments.
Stainless steel 2205 Duplex is the strongest stainless steel alloy (twice that of other ordinary stainless steel alloys) and has excellent corrosion resistance. It is used in harsh environments and has many applications in the oil and gas industry.
Compared with 304, 303 stainless steel has excellent toughness, but low corrosion resistance. Due to its excellent machinability, it is commonly used in high-volume applications, such as the manufacture of nuts and bolts for aerospace applications.
The mechanical properties of stainless steel 17-4 (SAE 630 grade) are equivalent to 304. It can be precipitation hardened to a very high degree (comparable to tool steel), and has excellent chemical resistance, making it suitable for very high-performance applications, such as the manufacture of turbine blades.
3. Low carbon steel
Low carbon steel has good mechanical properties, good machinability and good weldability. Due to their low cost, they can be used for general-purpose applications, including the manufacture of machine parts, jigs and fixtures. However, mild steel is susceptible to chemical corrosion and erosion.
Low carbon steel 1018 is a general-purpose alloy with good machinability and weldability, as well as excellent toughness, strength and hardness. It is the most commonly used low-carbon steel alloy.
Low carbon steel 1045 is a medium carbon steel with good weldability, good machinability, high strength and impact resistance.
Low carbon steel A36 is a common structural steel with good weldability. It is suitable for various industrial and construction applications.
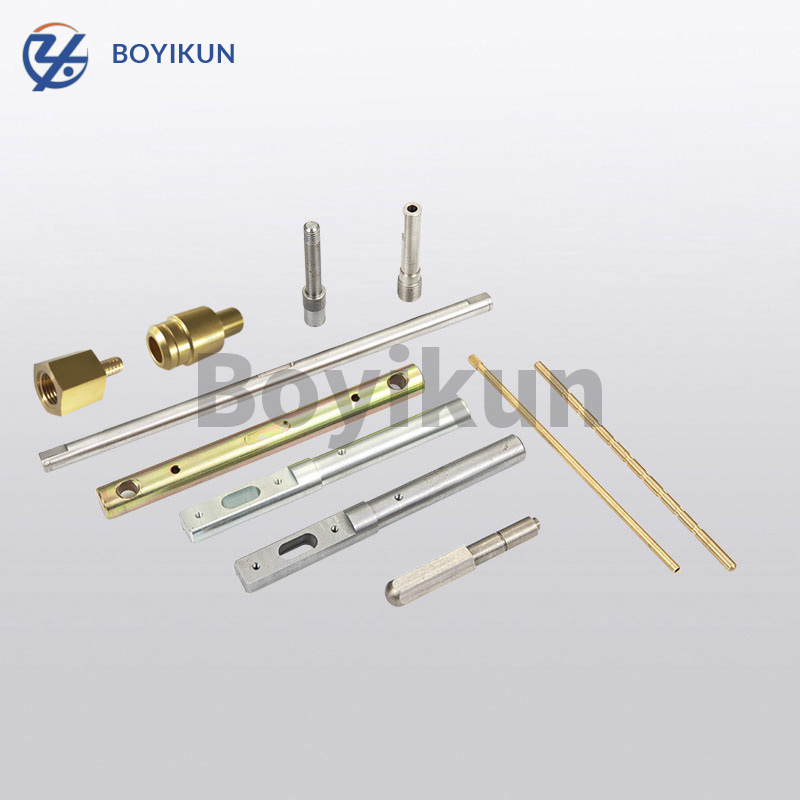
4. Alloy steel
In addition to carbon, alloy steel also contains other alloying elements, thereby improving hardness, toughness, fatigue and wear resistance. Similar to low carbon steel, alloy steel is susceptible to corrosion and chemical attack.
Alloy steel 4140 has good comprehensive mechanical properties, good strength and toughness. This alloy is suitable for many industrial applications, but it is not recommended for welding.
Alloy steel 4340 can be heat treated with high strength and high hardness while maintaining its good toughness, wear resistance and fatigue strength. This alloy is weldable.
5. Tool steel
Tool steel is a metal alloy with extremely high hardness, rigidity, wear resistance and heat resistance. They are used to make manufacturing tools (hence the name), such as molds, stamps, and molds. In order to obtain good mechanical properties, they must be heat treated.
Tool steel D2 is a wear-resistant alloy that can maintain its hardness at a temperature of 425°C. It is usually used to make knives and molds.
Tool steel A2 is an air-hardening general-purpose tool steel with good toughness and excellent dimensional stability at high temperatures. Commonly used to make injection molds.
Tool steel O1 is an oil-hardened alloy with a hardness of up to 65 HRC. Commonly used for knives and cutting tools.
6. Brass
Brass is a metal alloy with good machinability and excellent electrical conductivity, making it very suitable for applications requiring low friction. It is also commonly used in architecture to create parts with a golden appearance for aesthetic purposes.
Brass C36000 is a material with high tensile strength and natural corrosion resistance. It is one of the easiest materials to process, so it is usually used for high-volume applications.