Abstract:The concepts of component interchangeability and dimensional...
The concepts of component interchangeability and dimensional tolerances have become a recognized part of the manufacturing industry. Unfortunately, the misuse of the latter can cause a series of problems. For example, too tight tolerances may require parts to undergo secondary grinding or EDM operations to complete, thereby unnecessarily increasing costs and lead times. "Too loose" tolerances or inconsistencies with the tolerances of mating parts may result in inability to assemble, resulting in the need for rework, and in the worst case, the finished product cannot be used.
To avoid these unpleasant situations, this design technique includes some guidelines on how to properly apply part tolerances, as well as the definition of some more commonly used annotations. We will also discuss the industry standard for part tolerances, called Geometric Dimensions and Tolerances (GD&T).
1. Standardized tolerances of CNC machining
Assume that the standard prototype and production processing tolerances are +/-0.005 inches (0.13 mm). This means that the deviation of the position, width, length, thickness or diameter of any part feature from the nominal value will not exceed this value. If you plan to process a 1 inch (25.4 mm) wide bracket, the size will be between 0.995 and 1.005 inches (25.273 and 25.527 mm), and the bracket has a 0.25 inch (6.35 mm) hole on one leg, then the diameter of the bracket 0.245 to 0.255 inches (6.223 to 6.477 mm)
This is very close, but if you need higher precision, you need to judge based on the geometry and material of the part, please make sure to indicate it in the part design when uploading the file for quotation.
2. CNC machining tolerance guide
Also, please note that these are bilateral tolerances. If expressed in unilateral terms, the standard tolerance should be +0.000/-0.010 inches (or +0.010/-0.000 in.). All of these are acceptable, as are the metric values, as long as you specify in the design. To avoid confusion, please follow the "three-position" dimensions and tolerances shown, and avoid an extra zero position of 1.0000 or 0.2500 inches. Unless there is an absolute reason to do so.
3. Precautions for surface roughness of machining tolerances
In addition to length, width, and hole size, there are also part tolerances such as surface roughness. In the standard product, the surface roughness of flat and vertical surfaces is equal to 63 µin. A curved surface equal to 125µin is better.
For most purposes, this is a sufficient finish, but for decorative surfaces on metal parts, we can usually improve the appearance by light blasting. If you need a smoother surface, please indicate in your design and we will try our best to meet your requirements.
4. Geometrical dimensions and tolerances
There is one more consideration. As mentioned earlier, we can accept GD&T tolerances. This provides a deeper level of quality control, including various part features and the relationship between shape and fit qualifiers. Here are some of the more common methods:
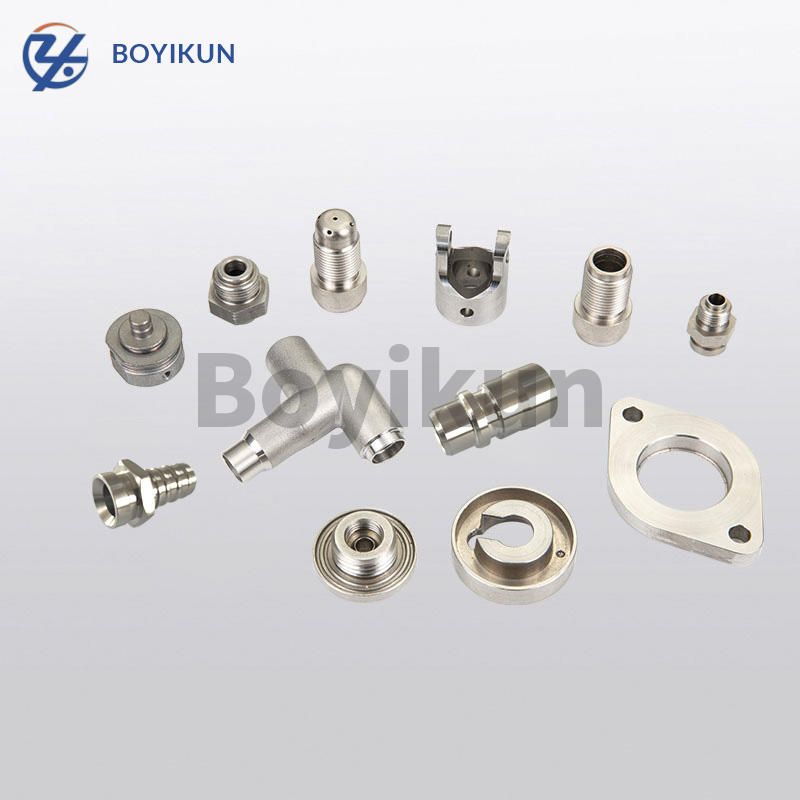
Real position: In the bracket example cited earlier, we mark the hole position by specifying the X and Y distances and their allowable deviations from a pair of vertical part edges. In GD&T, the position of the hole will be represented by the true position of a set of reference datums, accompanied by the qualifier MMC (Maximum Material Condition) or LMC (Minimum Material Condition).
Flatness: The
CNC milling parts is usually very flat, but due to internal material stress or clamping force during processing, some warping may occur after the parts are removed from the machine, especially thin-walled and plastic parts. The GD&T flatness tolerance controls this by defining two parallel planes in which the milling surface must lie.
Cylindricity: For the same reason, most milled surfaces are very flat, most holes are very round, and the same is true for turning surfaces. However, using a tolerance of +/-0.005 inch (0.127 mm), the 0.25 inch (6.35 mm) hole in the bracket example may be rectangular, and the other one-way dimensions are 0.245 inch (6.223 mm) and 0.255 inch (6.477 mm). The use of cylindricity is defined as two concentric cylinders in which the machined hole must be located. The manufacturer can eliminate this unlikely situation.
Concentricity: The rings on the bullseye are concentric, just like the wheels and axles of a car are concentric. If the drilling or reaming must be exactly the same as the coaxial counterbore or circular boss, the concentricity marking is the best way to ensure this.
Verticality: As the name implies, verticality determines the maximum deviation between the horizontal processing surface and the nearby vertical surface. It can also be used to control the perpendicularity of the turning shoulder to the adjacent diameter or the central axis of the part.